Semiconductor Industry
SEMICONDUCTOR INDUSTRY CHALLENGES
The semiconductor industry powers the systems and products we use to work, communicate, travel, entertain, harness energy, treat illness, generate new scientific discoveries, and so much more. Semiconductors, sometimes referred to as integrated circuits (ICs) or microchips, have been a major force in accelerating advancements in communications, transportation, and clean energy, among other fields.
The rapid pace of innovation has enabled the semiconductor industry to produce exponentially more advanced products at a more cost-effective level. With growing demand, semiconductor manufacturers face critical goals and tough challenges.
Some of the most common pain points focus on decreasing leachables, reducing friction and contamination, extending life performance, decreasing wear, improving sealability, reducing stick-slip, and simplifying design.
HIGH-PERFORMANCE POLYMER PRODUCTS FOR SEMICONDUCTOR APPLICATIONS
Semiconductors, which contain tens of billions of transistors on a quarter-sized piece of silicon, are fostering the development of new technologies that can revolutionize society for the better, such as brain-inspired computing, virtual reality, and artificial intelligence. The greatest potential for semiconductors is truly yet to come.
The highest quality, high-purity materials are paramount to meeting the demands of semiconductor innovation and transformation. The semiconductor industry relies on high-performance materials like thermoplastics, elastomers, and fluoroelastomers for numerous applications, including chemical mechanical polishing (CMP), wet cleaning and surface preparation, etching, vacuum pumps, wafer handling, electroplating, deposition, and valves.
Here is a sample of the many products manufactured using high-performance polymer products for the semiconductor industry:
- Optiseals
- Chemical Delivery Unit Seals
- Filtration Cartridges
- Valve Seals
- Pump Seals
- Flow Controller Seals
- Sight Glass Seals
- Heat Transfer Equipment Seals
Trusted High-Performance Polymers for Semiconductor Applications
The semiconductor industry has strict requirements and challenging specifications all driven to ensure optimal chemical resistance, thermal stability, and plasma resistance. To work with the leaders of industry, polymer product manufacturers must deliver the best quality materials and compounds, often focused on ultra-pure elastomers.
Ultra-pure elastomers like FKM and FFKM have some tangible benefits including decreased wet clean or mechanical clean frequency, minimized cost of consumables, increased mean time between failure (MTBF), and extended system uptime.
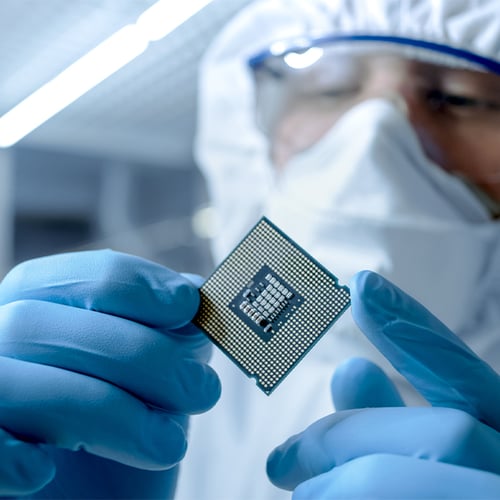
Some of the other materials in CDI’s material portfolio with the right characteristics and properties for semiconductor applications include:
- FKM - Fluorolex FHP-1
- FKM - Fluorolex FHP-3
- FKM - Fluorolex FHP-4
- FKM - Fluorolex FHP-5
- FFKM - Fluorolex FHP-2
- PTFE (Polytetrafluoroethylene)
Commonly Used Manufacturing Processes for Semiconductor Applications
With the highly critical nature of components and products for semiconductor applications, manufacturing of those products must meet the highest level of safety, quality, and reliability. With vertically integrated manufacturing, CDI provides far more than mere part production. With over 30 polymer manufacturing processes, our team of skilled machinists, operators and technicians use cutting-edge processes, and technology to manufacture the highest quality seals, wear products, and functional components.
Backed by extensive research, testing, and manufacturing capabilities, our design and development team often work together with our customers to design performance polymer products which meet the unique application specs and environmental conditions.
In the semiconductor market, some of the most used manufacturing processes include Class 1000 clean room molding, compression molding, injection molding, isostatic molding; transfer molding, CNC turning, CNC milling, manual machining, rubber machining, melt and ram extrusion, large diameter capabilities, thermoforming, overmolding, and bonding.