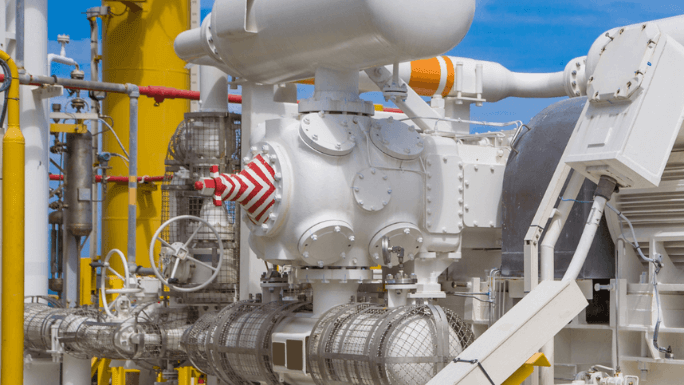
Packing Case Failures in Reciprocating Natural Gas Compressors
Posted by CDI Products on Feb 15, 2023
Reciprocating natural gas compressors are vital components in the natural gas industry. They are used to increase the pressure of natural gas for transportation and storage. Let’s look at the basic functionality for a natural gas compressor. These compressors use a piston that reciprocates within a cylinder to compress the gas, which is then dynamically sealed on the crank end by a packing case. The packing case contains a packing ring set to prevent leakage between the cylinder and the atmosphere.
Due to the critical nature of the compressor, packing case failures in any form can have significant impacts on efficiency and safety of the unit. In this article, we will discuss the leading causes of packing case failures in reciprocating natural gas compressors and the importance of proper installation, maintenance, and material selection to prevent these failures.
Improper Installation and Maintenance
One of the leading causes of packing case failures is improper installation and maintenance of the packing and/or the case. When installing packing in a reciprocating compressor, it is important to ensure that the correct type and size of packing is used for the specific application. Most OEMs specify exactly what kits or rings sets should be used for a given application as well as specify tolerances for the rebuild and repair of cases. The ring sets should be installed in a manner that ensures proper compression and prevents leakage. This includes proper installation of the ring sets, proper alignment of the compressor piston, and proper tightening of the gland bolts.
Proper installation is crucial in preventing packing case failures, as an incorrectly installed packing will not function as intended, resulting in leakage and reduced efficiency. The most common forms of incorrect installation include:
• Installing the ring sets in backwards in the case
• Installing ring sets out of order in the case
This will result in the packing not properly seating against the rod resulting in the rings not being compressed properly, ultimately allowing gas to leak past the piston rod. Similarly, if the flange bolts are not tightened properly, the packing case nose gasket will not seat against the stuffing box bore, again resulting in leakage. It is also important to check the alignment of the compressor piston, as a misaligned piston can cause uneven wear on the packing, leading to leakage and reduced efficiency.
Proper maintenance is also crucial in preventing packing case failures. This can include:
• Regularly lubricating the packing
• Replacing the packing when it becomes worn
• Checking for signs of leakage or wear between the cups
Proper lubrication to the packing is critical in reducing friction and wear and extending the life of the packing. It is also important to replace the packing when it becomes worn, as worn packing will not seal. Regularly checking for signs of leakage or wear can also detect potential issues before they become major problems, allowing for timely maintenance and repairs. It’s important to note: Packing case rebuilds should be performed using OEM specified packing and repaired by a qualified service facility that will machine and lap the packing cups to the OEM spec and light band test flatness tolerance and or pressure test the packing case for leakage before being returned. Any qualified repair facility should be able to produce a repair report that includes the OEM specifications, repaired specifications, part numbers of the OEM parts installed, as well as testing procedures and results for the repair.
Regular monitoring of the condition of the packing and the compression process can also detect potential issues before they become major problems. This may include:
• Monitoring the compression ratio
• Checking for signs of leakage
• Visually inspecting the packing for wear or damage
Monitoring the compression ratio can provide an indication of the efficiency of the compression process, and any deviation from the normal compression ratio may indicate a problem with the packing. Similarly, checking for signs of leakage can detect any issues with the packing, allowing for timely repairs.
Material Selection
Material selection for the ring sets is also an important factor in preventing packing case failures. The material used for the ring sets must be able to withstand the high pressure and temperature conditions of the compression process. Filled PTFE materials, PEEK, cast iron and bronze are commonly used materials for ring sets. Factors such as pressure, temperature, rod material, surface finish, and the chemical composition of the gas being compressed should all be taken into consideration when selecting a material for the ring sets.
Carbon and graphite are commonly used for low pressure applications and are known for their durability and resistance to wear. Filled PTFE materials are a popular choice for high-pressure applications due to their excellent chemical and temperature resistance properties. Metals such as cast iron and bronze are common in many applications, as they provide excellent durability.
It is important to choose the right material for the specific application as well as the conditions that the compressor will be operating under. For example, if the gas being compressed contains corrosive elements, a material with good corrosion resistance properties would be necessary. Similarly, if the compressor will be operating in high temperature conditions, a material with good heat resistance properties would be required. In addition to these properties, it is also important to consider the mechanical properties of the material, such as its strength, hardness, and wear resistance. For example, a material that is harder and stronger will be more resistant to wear and have a longer life span. It's also important to note that the ring sets material should be compatible with the lubricant that is being used. Incompatible materials and lubricants can cause chemical reactions leading to corrosion, wear, or damage in the ring sets.
Quality and cost of the material also play a factor when deciding on suitable material for an application, some materials are more expensive than others, but provide better performance and extended runtime over a lower cost material. Reliability engineers should weigh the quality of the material and cost against the expected performance and runtime of the ring sets to decide which material is the best fit for the specific application. Innovation in material technology, engineering capability, advanced manufacturing processes are critical when it comes to manufacturing quality parts that meet OEM specifications. OEMs rely on industry experts such as CDI to advise and provide materials and sealing technologies that lead to industry breakthroughs in emissions reductions, runtime, and reliability.
In conclusion, proper installation, maintenance, and material selection are key in preventing packing case failures in reciprocating natural gas compressors. Engineers should ensure that the correct type and size of packing is used and installed properly, lubricate the packing regularly and monitor the compression to detect any potential issues. Additionally, they should also ensure that the right material is selected for the ring sets that can withstand the conditions of the application. The material should also have the appropriate mechanical properties, such as strength, hardness, chemical resistance, and wear resistance, to ensure longer runtimes. Engineers should also consider the quality and cost of the materials and weigh it against the expected performance and life span of the ring sets. Regular monitoring and maintenance can detect potential issues before they become major problems and ensure efficient and safe operation of the compressor.
The bottom line - if you don’t schedule time for maintenance, your equipment will schedule it for you.
How Can CDI Help?
The compressor industry dates back over 350 years, but advancing capabilities and improvements, in both energy and power, mean that quality components for compressors are increasingly more critical and demanding. Our engineers understand the dynamic challenges and offer diagnosis assistance to find the root cause for problems and outline new solutions for optimum compressor performance. CDI’s extensive material library offers over 750 different materials to choose from. Our material developments are aimed at reducing wear and friction and improving mechanical properties, delivering greater compressor reliability and longer service life. In combination with our in-house blending capability, materials testing lab, and material engineers, CDI has a material for even the harshest applications. We are the trusted provider to some of the largest compressor companies in the global market, delivering compressor components including Piston Rings, Rider Rings, Packing Rings, Oil Wipers, Packing Cases, Compressor Valve Components, Poppets, Plates, Rings and much more. Contact us today to learn more.
Topic: compressors, reciprocating compressors, natural gas, packing case