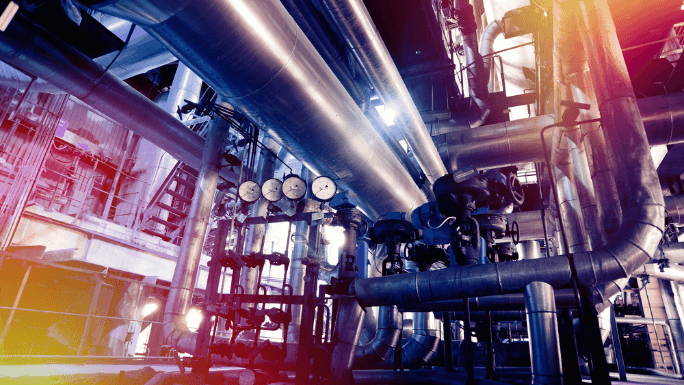
How Seals Combat HPHT
Posted by CDI Products on Mar 22, 2023
High-pressure, high-temperature (HPHT) environments are challenging for many engineering systems, and seals are no exception. Seals are essential components in a wide range of applications including:
- Aerospace power and fuel management
- Oil and gas drilling, completions, hydraulic operations and acidizing procedures
- Industrial power generation, transmission and distribution, fluid control, lubrication and energy management systems
- Medical devices, labware and diagnostic equipment
- Clean water management, thermal process equipment and filtration systems
Sealing elements in an HPHT well must be thermally resistant while also resisting extreme pressure. While all seals must be resistant to produced fluids such as oil-based mud, high pH fluids, amine base inhibitors, natural gas (CH4), water, seawater, and even hydrogen sulfide (H2S), in an HPHT environment, these fluids may be even more aggressive. Seals operating in HPHT environments must withstand extreme conditions that can cause degradation, deformation, and failure. This blog article explores how seals combat HPHT challenges and deliver the seal integrity essential for operational efficiency in these elevated pressures and temperatures.
What are HPHT Environments?
The rising demand for energy is driving the oil and gas industry to recover more challenging reserves, which can involve deeper and more aggressive downhole conditions. These deep reservoirs require a higher level of technologies and materials to withstand the local environment. HPHT environments expose seals to high pressures and temperatures, typically exceeding 10,000 psi and 150°C, respectively. Such environments occur in many industrial processes, including high-pressure pumps, valves, and compressors, as well as downhole drilling and completion operations in the oil and gas industry. In addition, HPHT conditions are present in some biomedical and material science applications, such as autoclaves and high-pressure reactors.
Why Do Seals Fail in HPHT Environments?
Seals can fail in HPHT environments due to various reasons, including:
- Thermal degradation: High temperatures can cause the seal material to decompose, leading to loss of elasticity and mechanical strength. Cracking may occur on surfaces exposed to the highest temperature ranges.
- Chemical attack: Some chemicals present in the environment can react with the seal material, causing swelling, cracking, or softening.
- Extrusion and deformation: High pressures can cause the seal to extrude or deform, reducing its sealing effectiveness and leading to leakage.
- Wear and abrasion: The high velocity of fluids or particles in the HPHT environment can cause wear and abrasion of the seal surface, reducing its lifespan.
- Rapid Gas Decompression (RGD): Gases forced into the sealing element may be unable to escape during system decompression. This could result in the seal being partially or completely destroyed.
How Seals Overcome HPHT Challenges?
Seals designed for HPHT applications must address the above failure mechanisms and provide robust sealing performance in extreme conditions. Some of the key approaches used to overcome HPHT challenges include:
- Material selection: Choosing the right seal material is crucial to withstand HPHT conditions. Materials such as fluoroelastomers (FKM), and polyimides have high-temperature resistance and chemical compatibility, making them suitable for HPHT environments.
- Seal design: The design of seals must consider factors such as extrusion resistance, wear resistance, and sealing effectiveness. For example, sealing elements with angled sealing faces can prevent the extrusion of the seal and improve sealing efficiency.
- Material combinations: Several materials can be merged to form a seal capable of handling HPHT conditions while offering effective sealing and anti-extrusion characteristics. Using PEEK back-up rings is one example, as they cover the extrusion gap, enabling elastomeric sealing elements to withstand greater pressures. PEEK back-up rings do not impact the surface finish when in contact with metal surfaces, unlike metal back-up devices. Additional materials include Polytetrafluorethylene (PTFE), Polyphenylene sulfide (PPS), and wire mesh components, which are all compatible with metal mating parts and suitable for various HPHT applications.
- Surface treatments: Applying coatings or surface treatments can improve the seals' wear and corrosion resistance in HPHT environments. Treatments such as diamond-like carbon and plasma spray coats can provide a hard and durable surface that resists wear and chemical attack.
- Testing and validation: Testing seals in simulated HPHT conditions is crucial to validate their performance and ensure reliability. High-pressure gas testing, compression set testing, and accelerated aging can simulate HPHT conditions and evaluate seal performance.
Seal Manufacturing for HPHT Environments
Manufacturing a robust seal that will be exposed to high-pressures and high-temperatures necessitates a careful thought. Seal profiles must be carefully chosen, as well as materials that are appropriate for these applications. This will ensure that equipment is deployed productively while maximizing mean time between maintenance (MTBM) intervals.
How Can CDI Help with HPHT Environments?
Seals are essential components in many engineering applications, but their performance in HPHT environments play a critical role. When you work with an experienced seal manufacturer like CDI, the seals must perform exceptionally and become a powerful barrier in the extreme environment it's designed to handle. We understand the challenges seal's face in HPHT environments and how the approaches used to overcome them can lead to improved seal designs and longer service life. Our experts assist companies by suggesting the right materials, designing seals for their particular HPHT application, applying surface treatments, and testing and validating their performance.
CDI Seals, Bearings and More
CDI seals and bearings can be found in many well completion tools, systems, and equipment, including:
• Liner Hanger seals
• Wiper Seals
• BOP Seals
• High-pressure pump packing
• Bonded seals
• Back-up rings
• Valve stem seals and seats
• Packer elements
• FS, OL, T, S, and LS Seals
• A6R Rotary Seals
• Tubing hangers
• Casing hangers
• V-Rings
• O-rings
• Header rings
Topic: header ring, o-ring, seals, HPHT, liner hanger seals, BOP seals, high pressure, high temperature