This guide explains the characteristics which are important when selecting a specific Arylast™ elastomer for use in a hydraulic system:
- Chemical Compatibility - Elastomer materials are more sensitive to fluids than other sealing compounds. Chemical reactions can cause damage to the seal, affecting physical properties. Selecting the proper elastomer material for a specific hydraulic fluid is critical. In addition to considering the oil, the additives added to the hydraulic fluids can cause adverse elastomer behavior. To counteract this, we may suggest conducting an immersion test at elevated temperatures to verify the application performance. Fluid Compatibility for commonly used aerospace fluids is located on the Elastomer Recommendations for Various Aerospace Hydraulic Fluids page.
- Temperature Range - Arylast™ compounds are available to operate in temperatures from -100°F (-73°C) to +500°F (+260°C). The majority of Arylast™ compounds will provide customers with elastomer choices that meet the temperature requirements of AS4716 type II systems, specified as -65°F (-54°C) to +275°F (+135°C).
- Temperature Cycling - The risk of temperature cycling an elastomer seal is that the elastomer can take a compression set. This means that the elastomer material loses its elasticity over time. For Arylast™ materials, this effect is minimized if they are used in the operating temperatures within the indicated parameters. The low-temperature dynamic cycling limits vary according to elastomer type.
- Cold Temperatures - Arylast™ materials are specially engineered to give maximum performance in cold conditions. In cold environments, elastomer materials contract approximately ten times more than steel materials. Elastomer materials also become stiffer and lose flexibility at cold temperatures. When passing the lower limit, an elastomer moves through the glass transition stage, when it becomes extremely brittle. Once the elastomer material is exposed to warmer temperatures, its physical properties will recover. Increasing the elastomer squeeze is a demonstrated method for enhancing low-temperature sealing performance.
- Hot Temperatures - If the elastomer's upper temperature limit is exceeded, the material becomes softer and loses its physical properties. Physical properties will not recover, and the seal will take on a permanent compression set. The type of media to which an elastomer is exposed can also affect its compressive set. Continuous exposure to temperatures above the prescribed range can irreparably damage the seal.
- Surface Speed - Each application should be evaluated on a case-by-case basis, in general, the speed of the dynamic surface in contact with an elastomer seal should be kept below 9.8 ft/s (3 m/s). This will avoid any damage to the elastomer.
- Aging - Each Arylast™ material has a maximum recommended storage time and shelf life, as shown in Table 1, per SAE AS5316. To achieve shelf life, Arylast™ seals shall be stored under controlled conditions in light-proof and airtight packaging.
- NBR (Nitrile Butadiene Rubber): AMS-P-83461 versus MIL-PRF-25732 - It is very important to separate these two NBR compounds because their chemical composition is unique, and their functional behaviors are optimized. This indicates that the recommendation for a static seal would be a seal made from AMS-P-83461 material while it would be recommended that a dynamic elastomer contact seal should be made from a MIL-PRF-25732 material. The recommendation for an elastomer used to energize PTFE seal would be an AMS-P-83461 material since the elastomer is energizing the PTFE and experiencing dynamic movement on the mating surface.
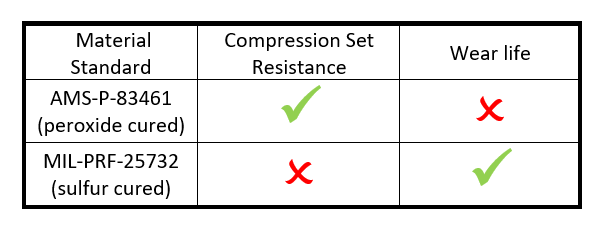