Transfer molding is a distinctive production method that combines the fundamentals of both injection molding and compression molding. Since its introduction, this technique has undergone substantial development, providing a multifaceted approach for the fabrication of components with high precision. Its uniqueness lies in its hybrid nature.
Industry Applications
- Aerospace: In aerospace, components must withstand extreme temperatures, pressures, and chemical exposures. Transfer molding is used to create high-precision, high-performance seals and gaskets that can endure these conditions.
- Oil and Gas: This industry requires components that can withstand harsh chemicals, high pressure, and abrasive environments. Transfer molded parts like seals and gaskets are essential for maintaining the integrity of equipment used in exploration, extraction, and processing.
- Semiconductor: The semiconductor industry demands parts with very high precision and purity. Transfer molding can produce parts that meet these stringent requirements, as it allows for tight control over material properties and reduces the risk of contamination.
- Pumps and Valves: These applications often require custom-shaped seals and gaskets that can withstand varying pressures and corrosive materials. Transfer molding is ideal for producing these durable, precisely shaped components.
- Reciprocating Compressors: In these systems, seals and gaskets must endure high pressure and repetitive motion. Transfer molded parts are favored for their durability and ability to maintain their properties under such stress.
- Power Generation: This sector, encompassing a range of environments from nuclear to coal-fired plants, requires robust and reliable sealing solutions. Transfer molding can produce parts that withstand high temperatures and aggressive substances.
- Renewable Energy: In industries like wind and solar power, the components may need to resist weathering, UV exposure, and temperature fluctuations. Transfer molded parts can be formulated to meet these specific environmental challenges.
- Hydrogen Industry: As a relatively new and rapidly evolving sector, the hydrogen industry requires innovative sealing solutions for storage and transportation of hydrogen. Transfer molding allows for the development of materials and shapes that are specifically suited for high-pressure and highly reactive environments.
Advantages
- Material Properties: The curing process at high temperatures allows for excellent dimensional stability and increased strength of the molded parts, making them suitable for high-performance applications.
- Intricate Designs: Transfer molding is ideal for creating parts with intricate details, tight tolerances, and inserts due to the use of pressure, ensuring the material fills complex mold geometries.
- Reduced Waste: Excess material often remains in the pot instead of the mold and can sometimes be reused, reducing overall material waste.
- High Production Rate: Although the setup can be complex, once operational, the process allows for a relatively high production rate compared to other molding methods.
Recommended Materials
- Polymers: Like polyurethane and fluoroelastomers (Viton), these are appreciated for their strength and chemical resistance.
- Rubber: Recognized for its elasticity and resilience.
- Plastics: Such as polypropylene and polycarbonate, chosen for their flow properties and chemical resistance.
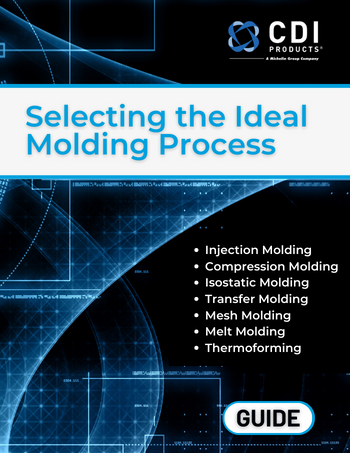
Don't leave your production goals to
chance - download the guide and take control
of your molding process selection today.
Other Molding Processes

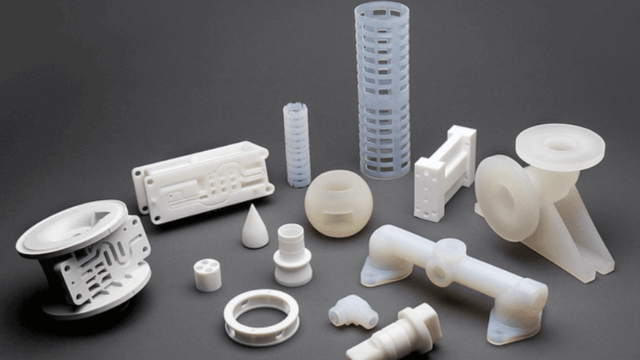